Metal Bellows expansion joints
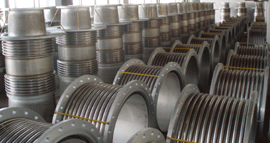
Metal bellows expansion joints are ubiquitous to heavy industrial markets. If there is fluid or gas movement, be it in the petrochemical, electric power supply, paper and pulp or a variety of OEM industries, optimal operation and "up-time" require state-of-the art piping systems to keep your plant competitive, or better, ahead of the curve. You know your business, and you know that in order to be profitable, your system must run at maximum efficiency. Metal Bellows Expansion Joints allow you to control fluid movement and containment in your system under a wide variety of pressures, thermal expansion and contraction, pulsations, vibration, equipment movement and convoluted routing requirements.
Typically, the key component of an expansion joint is the Metal Bellows element. Flexibility is paramount in containing the media and the pressure inherent in the system. Metal bellows expansion joints, thin-walled, corrugated membranes, provide this flexibility.
MATERIAL
304 (ASTM A240-304)
It is the most common grade and services a wide range of applications. It is thermal resistance, corrosion resistance, with nicer cold crushing strength and mechanical properties. Type 304 resists nitric acid and sulfuric acids at moderate temperatures and concentrations. Bellows supplied in this grade are usually used on water or steam applications.The temperature range varies from -162℃ to 648℃.
316 (ASTM A240-316)
The second most common grade (after 304); Alloy addition of molybdenum prevents specific forms of corrosion. It is also known as marine grade stainless steel due to its increased resistance to chloride corrosion compared to type 304. Some typical uses include high sulphur crude oils, brackish waters, flue gases ,food processing and numerous applications in chemical and petrochemical processing.
316L (ASTM A240-316L)
Extra low carbon grade of 316, generally used in stainless steel watches and marine applications due to its high resistance to corrosion.
321 (ASTM A240-321)
Similar to 304 but lower risk of Weld Decay due to addition of titanium, the addition of titanium also make it have better ability to prevent intergranular corrosion and high temperature resistance. The temperature of Type 321 is range from 426℃ to 890℃. The standard catalog exhaust joints are made from this material because of the high operating temperatures they withstand.
Alloy 800 (ASTM B409-800)
The application temperature of Alloy 800 is about 590℃.It has nicer ability of creep resistant , corrosion resistance and rapture stress resistant properties. No matter sub - zero ,indoor temperature or high temperature which below 600℃,it always has better mechanical properties. It is widely used in variety of difficult service conditions.
Comparison Chart of the material
CHINA
|
JAPAN
|
USA
|
GERMANY
|
GB1220-92
|
JIS G4303-91
|
ASTM A276-96
|
DIN 17400-96;DIN EN 10088-1-95
|
Cr+Ni
|
0Cr18Ni9 |
SUS304 |
304 |
X5CrNi18-10 |
1.4301 |
0Cr18Ni10Ti |
SUS321 |
321 |
X6CrNiTi18-10 |
1.4541 |
Cr+ Ni + Mo
|
0Cr18Ni13Mo2Ti |
SUS316 |
316 |
X5CrNiMo17-12-2 |
1.4401 |
00Cr17Ni13Mo2 |
SUS316L |
316L |
X2CrNiMo18-14-3 |
1.4404 |
Stainless Steel Designations
AISI
Designation
|
W.Nr.
Designation
|
% Cr |
% Ni |
% C |
% Mn |
% Si |
% P |
% S |
% N |
Other |
Austenitic |
304
|
1.4301
|
18–20
|
8–10.50
|
0.08
|
2
|
0.75
|
0.045
|
0.03
|
0.1
|
-
|
316
|
1.4401
|
16–18
|
10–14
|
0.08
|
2
|
0.75
|
0.045
|
0.03
|
0.1
|
2.0–3.0 Mo
|
316L
|
1.4404
|
16–18
|
10–14
|
0.03
|
2
|
0.75
|
0.045
|
0.03
|
0.1
|
2.0–3.0 Mo
|
321
|
1.4541
|
17–19
|
9–12
|
0.08
|
2
|
0.75
|
0.045
|
0.03
|
0.1
|
Ti 5(C+N) min, 0.70 max
|
|